HOW WE DO IT?
PRODUCTION PROCESS
1
SELECTION
Selection and harvesting of high-quality raw materials are done in the forests by our experts and partners of Exportdrvo.
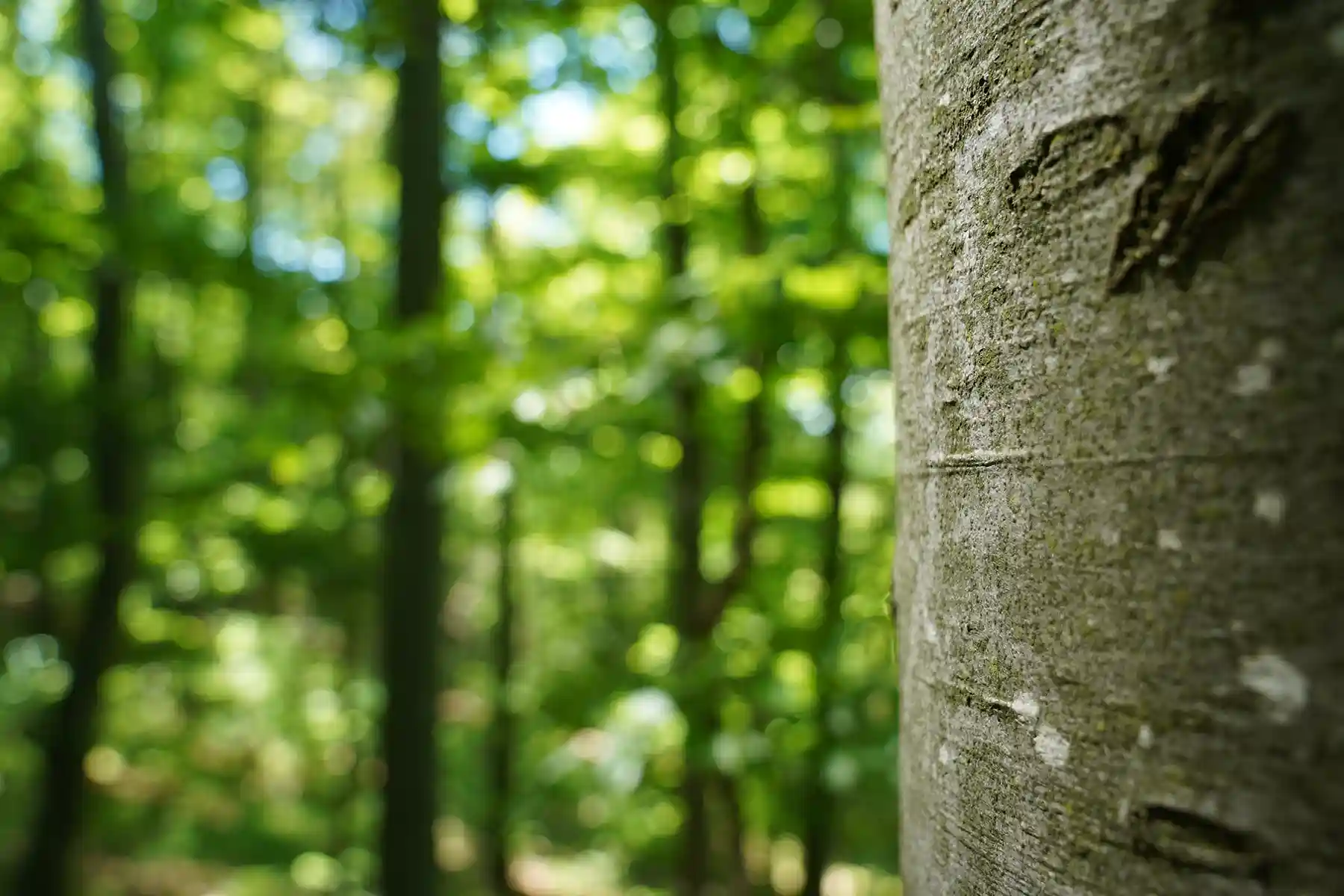
2
PREPARATION
Preparation of logs on the peeling line is the first step in the sawmill production process, followed by longitudinal shortening and sorting according to quality and diameters.
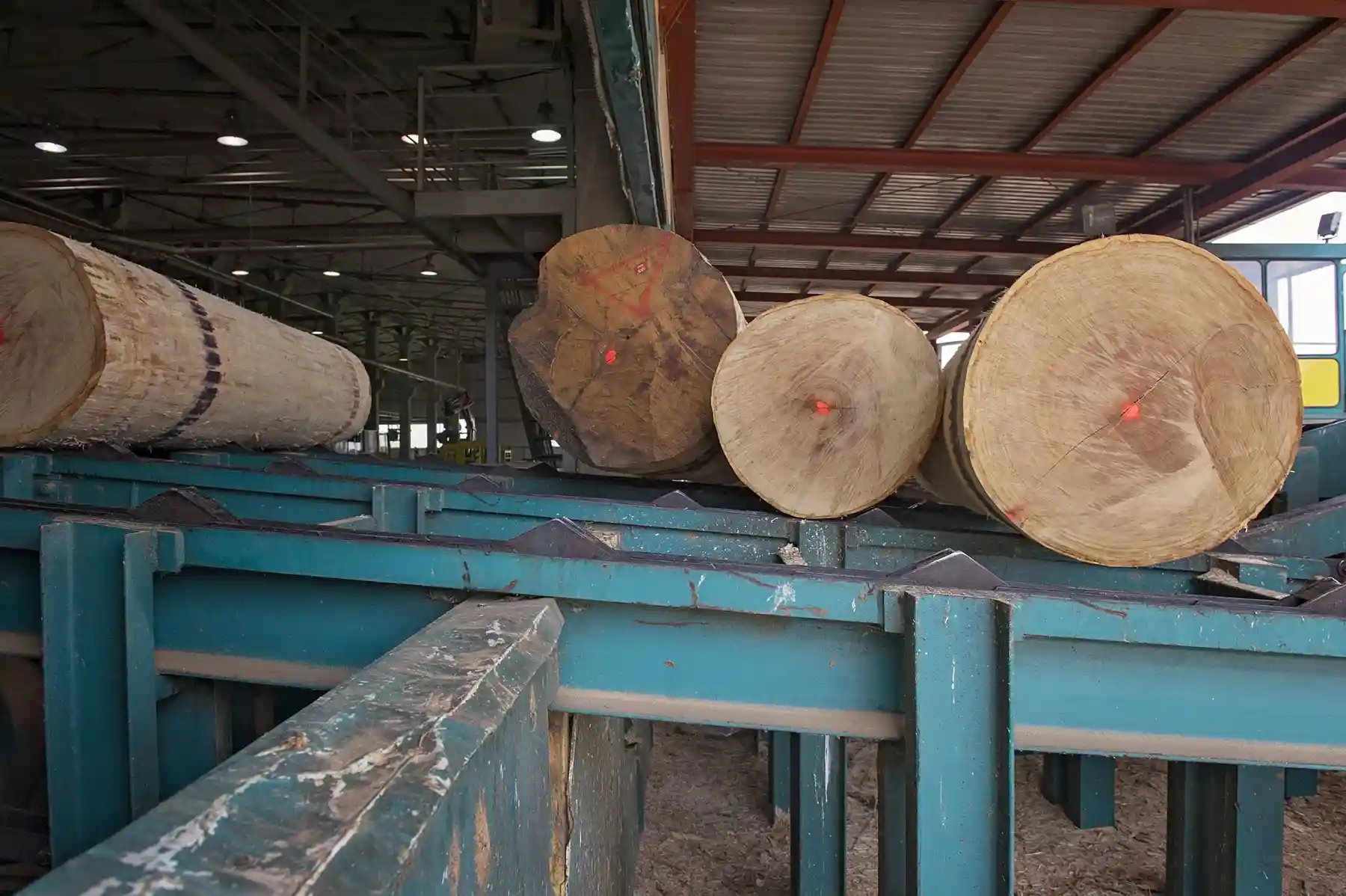
3
CONTROL
All logs are checked according to the degree ofquality and sorted according to grades and dimensions.
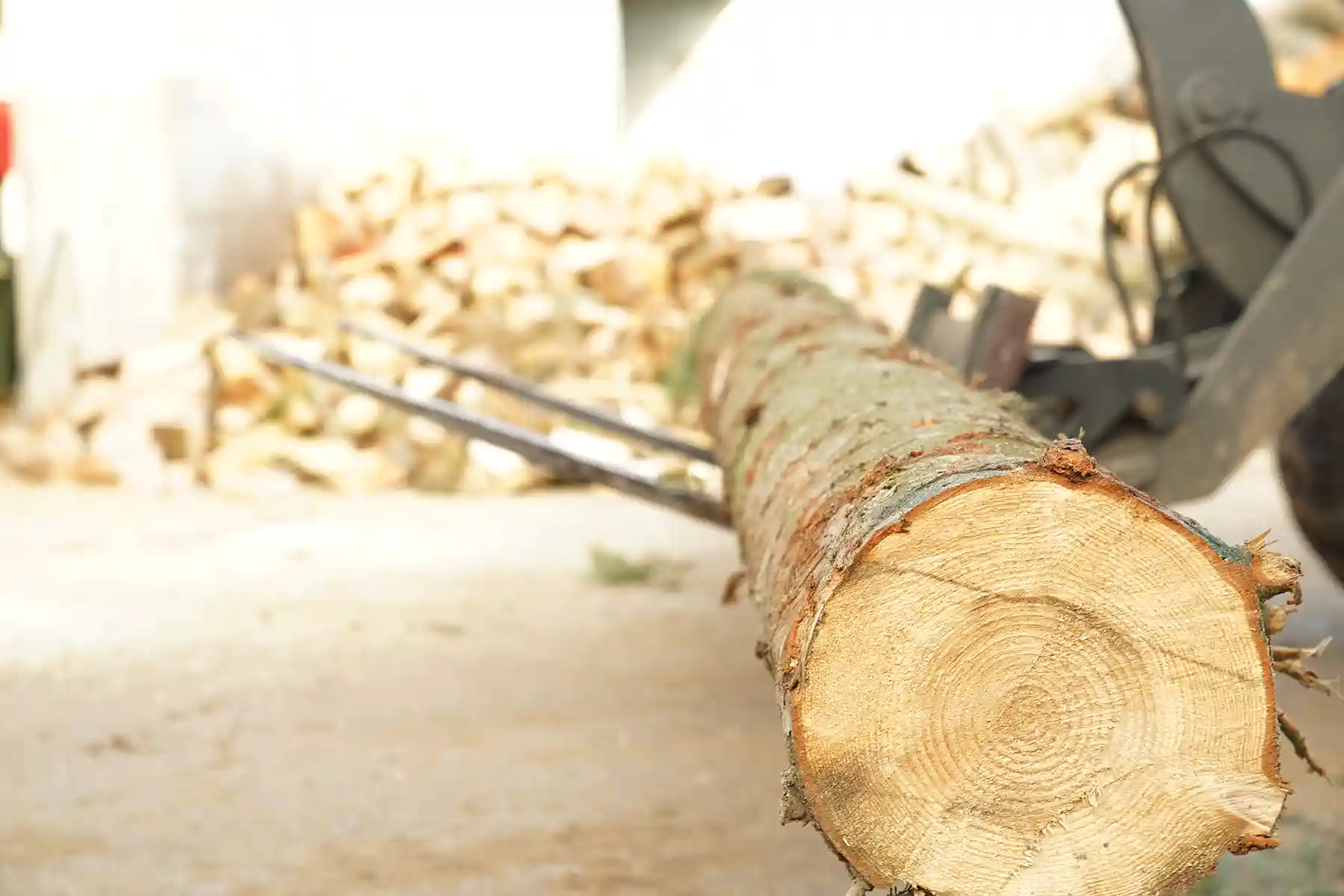
4
PROCESSING
The logs are processed in more than 70 sawmills with which Exportdrvo cooperates, with an annual capacity of over 250.000 m3.
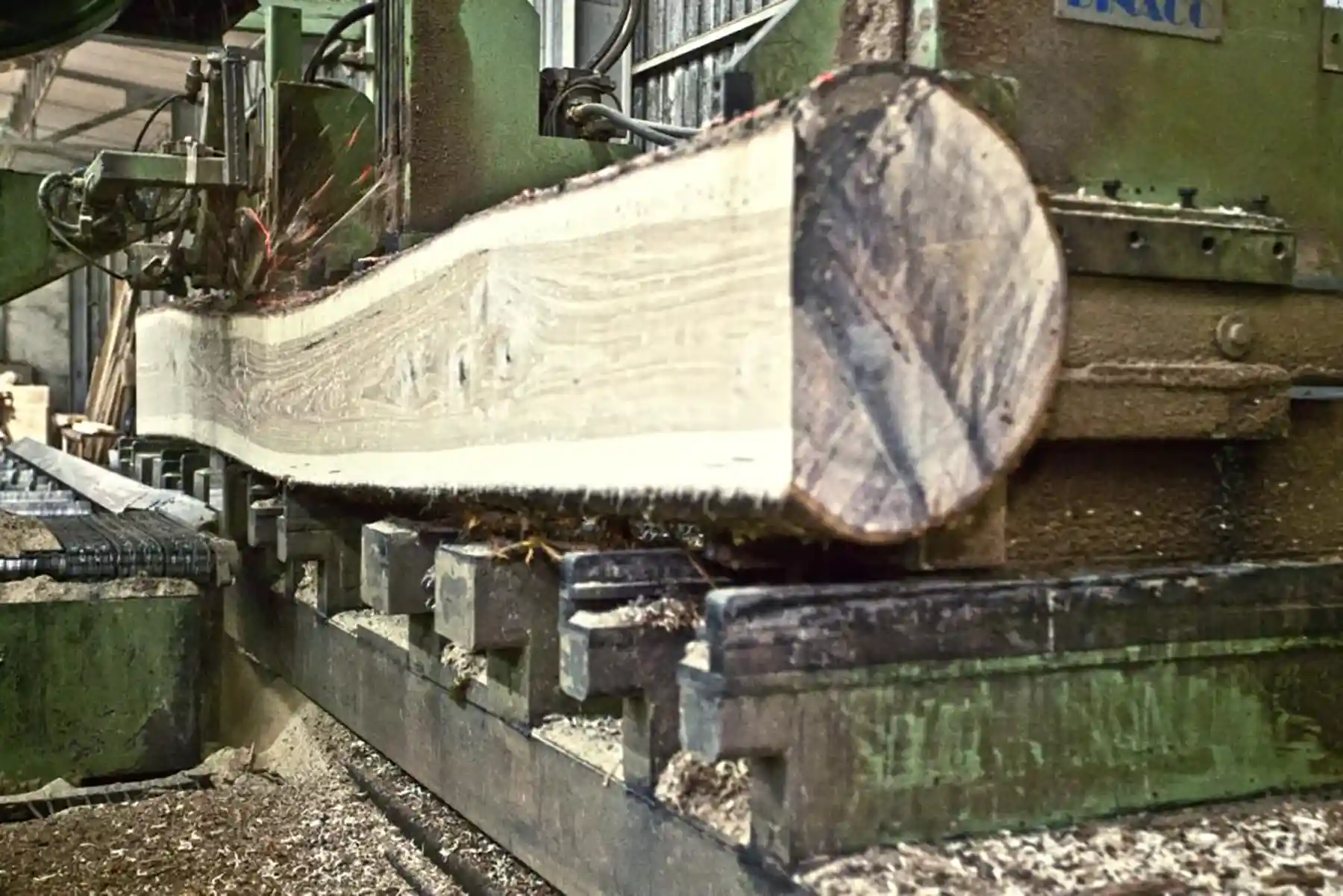
5
DRYING & STEAMING
Some wood, specifically beech, undergo steaming treatment before drying in modern dryers with a total capacity of 5.000 m3. The wood is dried to the desired humidity and then sorted according to the agreed grades.
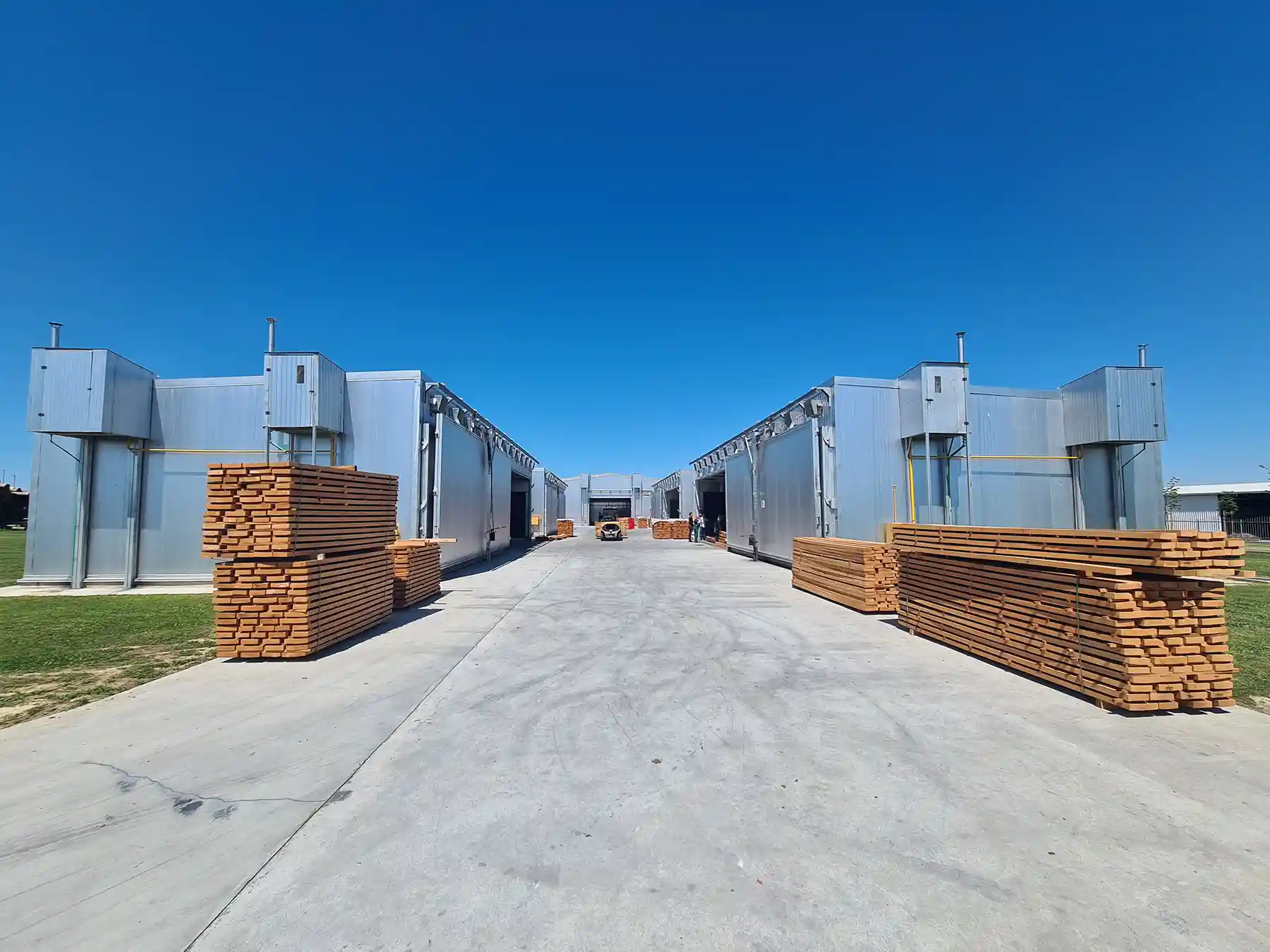
6
ANTI-STAIN
Anti-stain treatment is also offered to protect the wood from discoloring and increase durability.
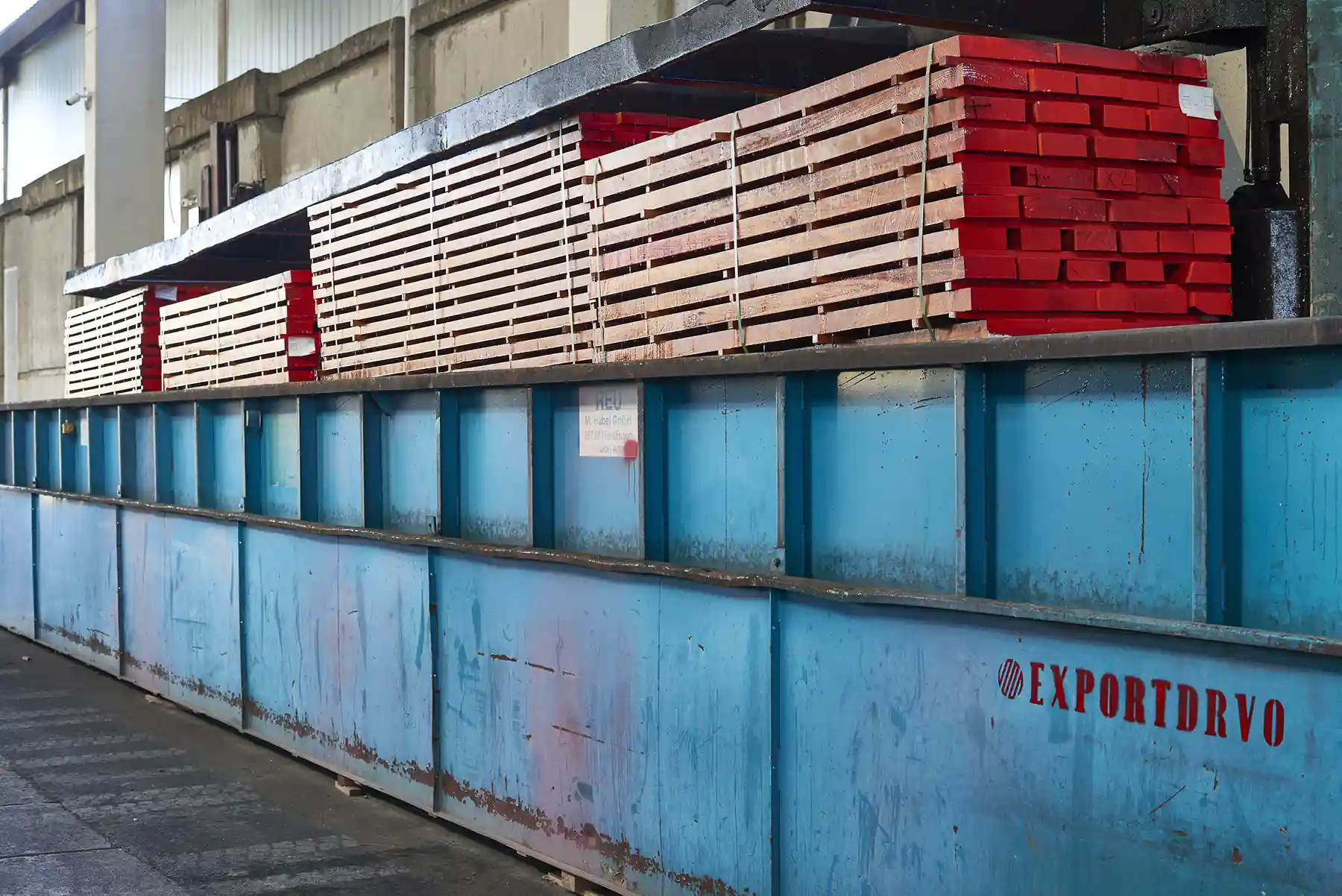
7
BRANDING
The final step in the production process is product branding and packaging, with each product clearly labeled with the recognizable Exportdrvo sign – synonymous for quality and reliability in the wood industry.
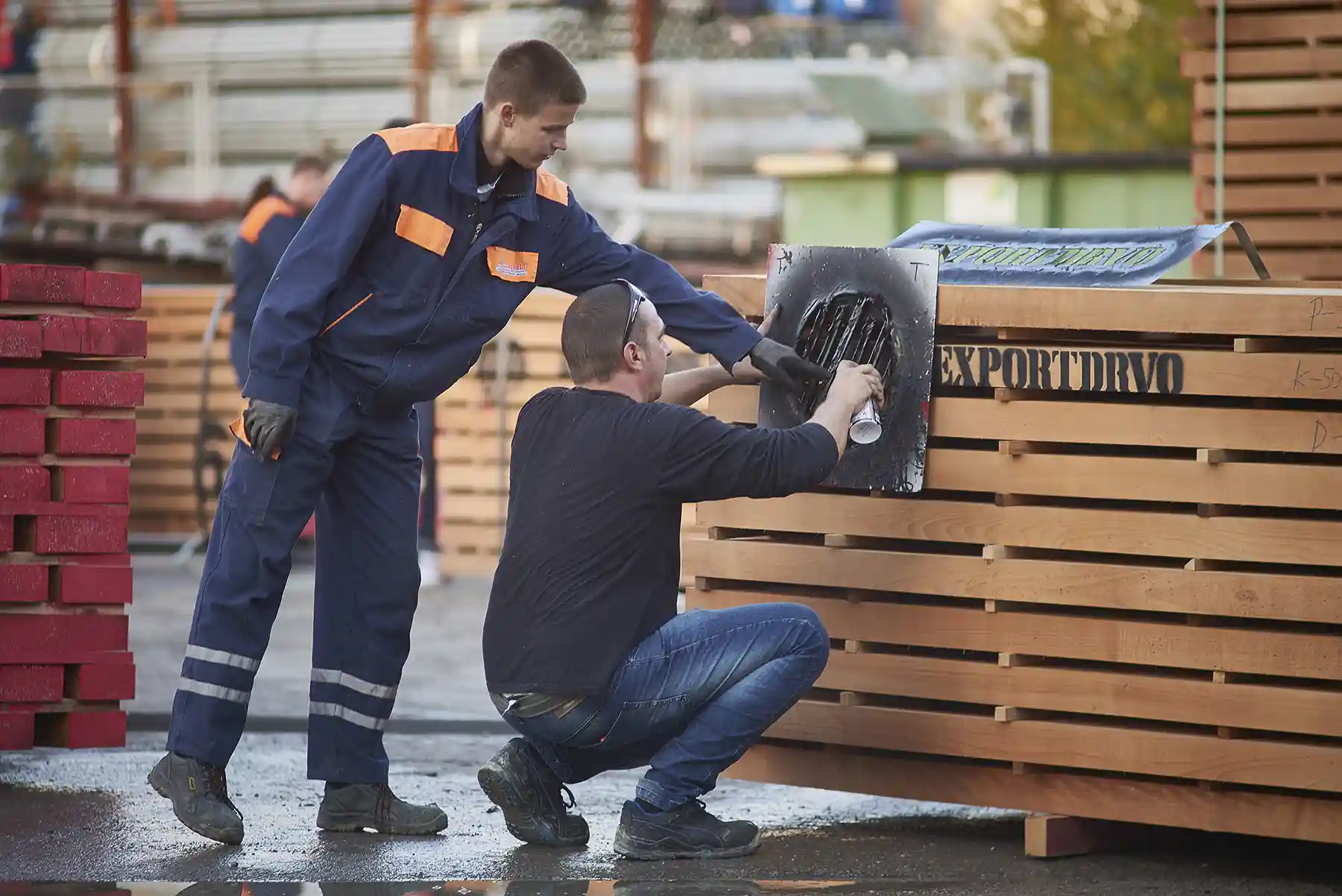
8
WAREHOUSING
All products are stored in covered warehouses with a capacity of over 30.000 m3, which meet the highest European standards and are delivered to the world market in the form of fresh, dried or dry timber and wood elements.
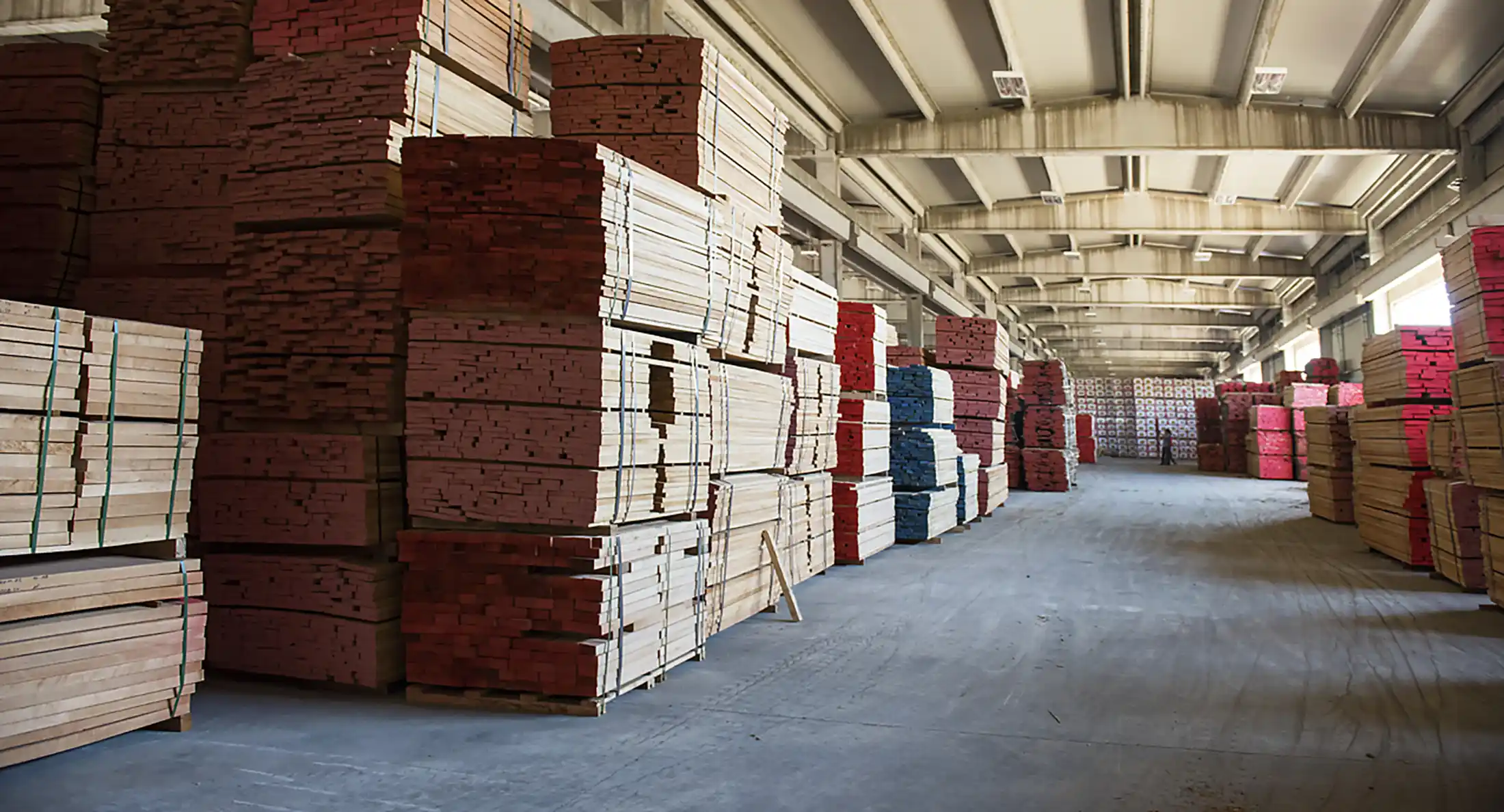
9
SHIPPING
Our sawn timber products are shipped to the world market by trucks, bulk ships, or container ships.
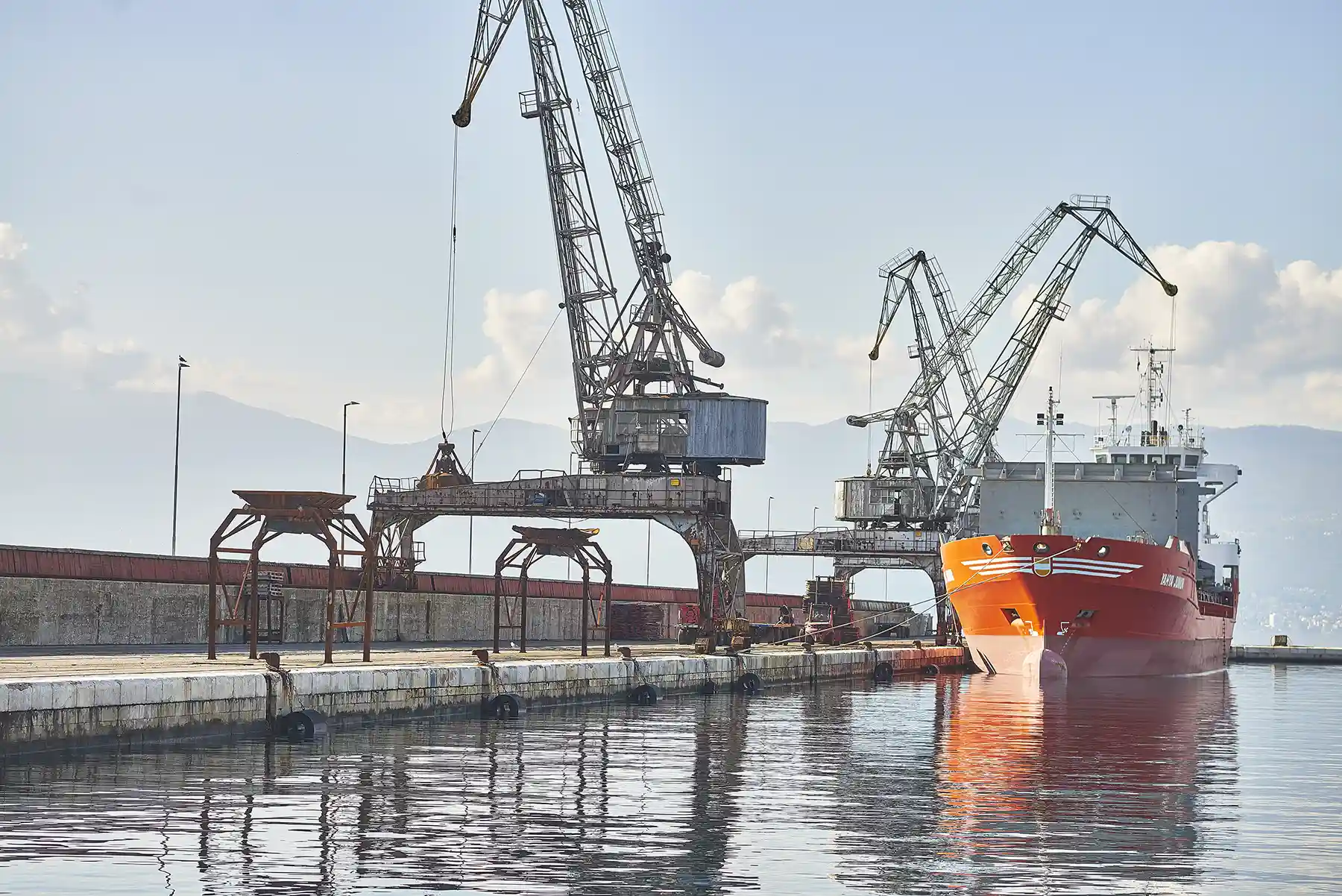